- Visitor:46
- Published on: 2024-11-20 05:06 pm
When Nadir Shah Met with Unyielding Defiance: How a 1300-Year-Old Iron Artefact Cocked a Snook at the Murderous Invader from Persia
No-one knows who exactly had built the iron pillar currently located in the complex. Based on the name ‘Chandra’ that figures in one of the inscriptions on it, the pillar is believed to have been forged at the behest of Chandragupta II Vikramaditya, the great Gupta emperor, about 1600 years ago. It is likely the pillar had been brought to the Qutb Complex from elsewhere by one of the early Sultans of Delhi to plant as a trophy.
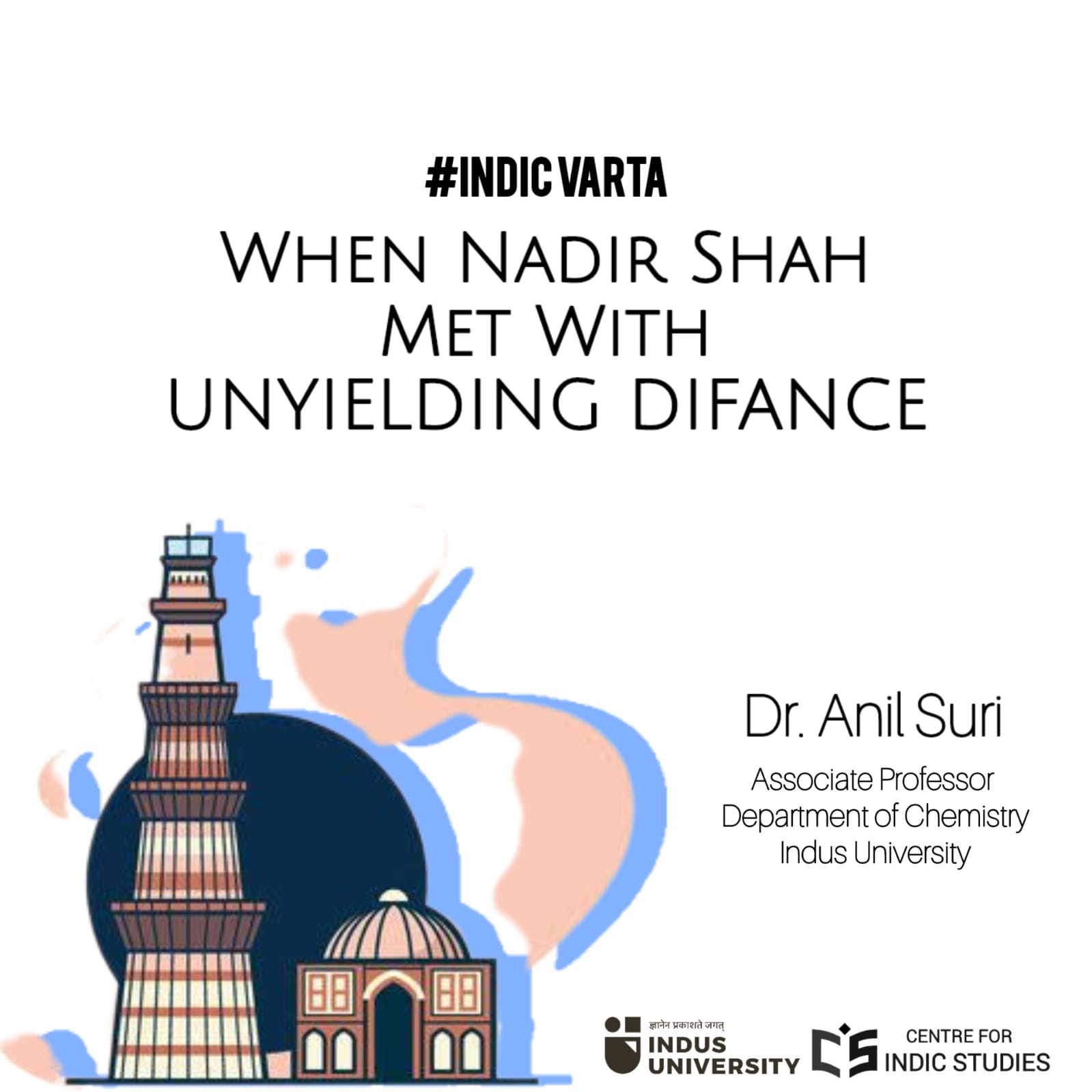
When the Persian invader, Nadir Shah, who occupied Delhi in 1739, visited the Qutb Minar complex, he was dismayed to find an artefact made by Kafirs (unbelievers) occupying pride of place. No-one knows who exactly had the iron pillar currently located in the complex made. Based on the name ‘Chandra’ that figures in one of the inscriptions on it, the pillar is believed to have been forged at the behest of Chandragupta II Vikramaditya, the great Gupta emperor, about 1600 years ago. It is likely the pillar had been brought to the Qutb Complex from elsewhere by one of the early Sultans of Delhi to plant as a trophy: the pillar is located in the courtyard of the Quwwat-ul-Islam (“Might of Islam”) Mosque. However, unlike the fragments of temples that had had any Hindu or Jain imagery defaced before being used in the Islamic structures in the complex, the iron pillar does not seem to have been changed in any noticeable way. This is probably what met with Nadir’s disapproval.
Not one to lose time, he lined up a cannon and had a ball fired at the pillar, believing – not unreasonably – that it would not survive the explosion. After the smoke from the gunshot had cleared away sufficiently, Nadir found, to his great shock, that the ancient iron pillar had not only withstood the impact of the cannonball but the ball had ricocheted off the pillar, and fallen on the Quwwat-ul-Islam mosque, destroying its southwestern wing in the process. One can see both the minor concave dent and a fissure in the pillar from the shot as well as the damaged portion of the mosque today. Nadir dared not fire a second ball at the pillar, lest it fall on him in its rebound. Nadir was not one to brook any defiance, having ordered an infamous general massacre of Delhi’s citizens when his soldiers faced minor skirmishes, which any hostile foreign army can expect. However, when it came to this ancient kafir artefact, he quietly decided that discretion was the better part of valour!
The corrosion-resistant Iron Pillar in the courtyard of the Quwwat-ul-Islam mosque in Mehrauli, Delhi (picture courtesy: Wikipedia).
“Rustless” Wonder
One is struck by the absence of any loose rust on the surface of the pillar, which hints that it has not been weakened by weathering in all the centuries that it has stood exposed to the elements. Compare this with the Eiffel Tower, whose rivets have to be changed every few years. Indeed, can you think of any stainless steel objects in your home that will not start rusting if they are immersed in water continuously for a few days (steel is basically an alloy of iron and carbon, and some other elements)?
However, the fact that the iron pillar has been so resistant to corrosion is not the only thing wondrous about it. The technology by which the pillar was forged to make it extremely strong – indeed so strong a cannonball barely dented it 1300 years after it was made – is remarkable too.
Sponge Iron and Forge-welding
Iron was traditionally made by what was known as the bloomery process. Pulverised iron ore, charcoal and a mixture of minerals known as fluxes - often other iron oxides occurring in the ore itself - were charged into a furnace. The charcoal would be partially oxidised to carbon monoxide, which would then reduce the iron ore to iron. To maintain a sufficiently high temperature in the furnace, the blacksmith would blow air through holes at the bottom of the furnace using bellows. If the temperature in the furnace rose very high, the charcoal would be oxidised to carbon dioxide, and no iron formation would happen. Thus, the fluxes, which catalysed the formation of iron at suitably low temperatures, and mopped up the molten byproducts and removed them in the form of slag, were extremely important. At the end of this process, the furnace would yield a welter of iron and slag, which is a mixture of all the byproducts of the reaction. This welter was known as a bloom. Some communities that smelted iron this way referred to this forbidding-looking mass as hagora (the furnace’s excreta). In order to get rid of the slag, the bloom, while still red hot, would be hammered to squeeze the as-yet semi-liquid slag out, leaving a pancake-shaped metal ingot with only microscopic inclusions of slag in it behind. The iron obtained in this way is known as sponge, bloomery or wrought iron. The iron could also contain a certain amount of carbon.
It is easy to appreciate that the process of iron making is unlikely to have been an accidental discovery. It comprises multiple steps, none of which are intuitively obvious. In other words, it could only have been the result of deliberate experimentation and probably took centuries to perfect. Archaeological evidence tells us that many parts of India had developed ironmaking processes by the early half of the 2nd millennium BCE, which is significantly earlier than elsewhere in Eurasia. Unfortunately, Western scholarship prefers to ignore this evidence, and take the ironmaking process developed in Anatolia (present-day Turkey) in around 1200 BCE as the starting point of ferrous metallurgy. It is also likely that ironmaking technology may have spread to India to other parts of Eurasia.
To make large objects, multiple pancakes of sponge iron were joined together by heating to a red-hot state and hammering them together. At the interface, the lumps would fuse together owing to localised melting. This process is known as forge welding. Indian blacksmiths preferred this process to casting for making large objects such as guns and pillars. Casting is more economical and straightforward, and can be easily scaled up for manufacturing large objects, but also requires temperatures high enough to melt the metal till it can be poured into a mould. Now Indian blacksmiths were perfectly capable of producing such high temperatures. So what was the reason for choosing the highly laborious forge welding?
Heating and hammering, as is done in forge welding, eliminates any pores or voids and produces a denser metal. It also produces a fine-grained microstructure, which leads to better toughness. The grains are also aligned, leading to high strength and impact resistance. In other words, products obtained by forge welding are of a much better quality than those produced by casting.
The dent and horizontal fissure on the Iron Pillar caused by Nadir Shah’s cannon shot. The Qutb Minar can be seen in the background. (Picture courtesy: Trip Advisor)
One may fear that, in an object produced by forge welding multiple blooms together, the large number of interfaces may make the object more liable to fail. However, it is a testament to the skill of Indian blacksmiths that the iron pillar, far from fragmenting along its multiple seams, behaved as an integral whole when fired upon by Nadir Shah’s gun – and this was nearly 1400 years after it had been forged and left exposed to the elements the entire time.
What is even more interesting is that the pillar is made from iron, and not steel. Steel is made by alloying iron and carbon. As a result of alloying, steel has better mechanical properties than iron, especially strength and toughness. The mastery of the blacksmiths over the forge welding technique is evident from the fact that the ancient pillar not only withstood the impact of Nadir’s cannonball suffering no more than a small dent and a minor fissure, but sent it ricocheting back.
Corrosion Resistance
The most immediately observable feature of the Iron Pillar is, of course, its resistance to rusting. This feature baffled scientists for a very long time, till it was finally understood by Prof. R. Balasubramaniam of the Indian Institute of Technology Kanpur. The technique for making the pillar resist corrosion has the simplicity of genius.
The pillar does have a thin layer of rust on it. Balasubramaniam analysed the rust, and found that it contained hydrated iron hydrogen phosphate. It is known that ancient iron produced by the bloomery process had a much higher phosphorus content than that made by modern processes. This is because many ores used from the ancient to mediaeval times contained phosphorus compounds, from which phosphorus made its way into the iron. Modern processes avoid phosphorus, as it makes the iron brittle; indeed, modern processes use limestone (calcium carbonate) as a flux, which removes phosphorus from the iron by forming calcium phosphate. However, traditional processes worldwide preferred phosphoric iron owing to its higher strength, even if it meant more brittleness.
While bloomery iron the world over had phosphorus, only the Indians exploited it to confer corrosion resistance on the iron. This was done by alternately wetting and drying the iron. When the phosphorus-containing iron was wet in the rain, rust (iron hydroxides) would form at the surface, leading to an increase in the content of phosphorus at the iron-rust interface. Each wetting/drying cycle would lead to a progressive enrichment of phosphorus at the interface, eventually leading to the formation of phosphoric acid owing to the reaction of phosphorus and water. The phosphoric acid would then react with the iron, leading to the formation of a contiguous, crystalline layer of hydrated iron phosphate at the interface. The hydrated iron phosphate acts as a passivating layer, which prevents further corrosion of the iron surface. Once this layer is formed, rain will not rust the iron any more.
It is a common observation that wetting leads to the formation of rust on iron surfaces. However, rust is a mixture of hydrated iron oxides and iron hydroxides, which are porous. They are not capable of stopping further corrosion of the iron: water can seep through the pores and attack more iron. The hydrated iron phosphate formed on phosphorus-containing iron, on the other hand, is continuous and impervious, and shields the iron from further rusting.
Again, it is easy to appreciate that this discovery is unlikely to have been entirely accidental. Only a systematic study of the effect of alternate wetting and drying cycles could have led to the discovery of corrosion-resistant iron. Indeed, many metals acquire a thin layer of oxide on their surfaces owing to the action of atmospheric oxygen. A prominent example is aluminium, which grows dull over time thanks to the formation of an oxide layer. This layer is continuous and is capable of passivation - it prevents further corrosion, even by strong acids. Yet other metals like magnesium and iron are unable to form a continuous oxide film which can protect them from corrosion.
Widespread Technology
For long, Western researchers argued that the absence of significant rusting on the Iron Pillar was not so much owing to any special properties of the metal as the relatively dry climate in Delhi. But such iron has been found in multiple places in India: the fragmented iron pillar in Dhar (Madhya Pradesh) the combined length of which is twice the height of the Delhi Iron Pillar, the iron frame of the Sun Temple in Konark (Odisha), the iron pillar in the Adi Mookambika Temple in Kodachadri (Karnataka), and numerous guns made by the Marathas that can be seen in their forts on the Konkan coast, such as the mighty Kalak Bangadi cannon in the Murud-Janjira fort. Indeed, Indus University is home to two excellent specimens of corrosion-resistant iron technology: the guns flanking the entrance to the main building. Many of these places experience heavy rainfall, and some are located on the coast, where the atmosphere is quite corrosive. Clearly, the resistance to rusting is not owing to a benign environment, and Prof. Balasubramaniam’s explanation is likely correct.
How did we lose this technology, which was widespread all over India as late as three hundred years ago? For this, we must blame the British, who were slowly beginning to produce large amounts of iron and steel and desperately needed markets to offload these on. However, the quality of British metal was no match for that of what was being produced in India. The only way the British iron and steel industry could survive was by banning Indian metal. This they proceeded to do by way of the cleverly disguised Forest Acts passed in the 19th century, which barred Indians from exploiting any resources from any piece of land that was classified as a forest - essentially, any land that was currently not under cultivation. Thanks to these Acts, Indian metalsmiths lost access to ore as well as wood for making charcoal that was required to smelt the ore. Almost overnight, thousands if not lakhs of people engaged in the trade were disenfranchised and brought to the brink of starvation. Today, the once prosperous traditional blacksmith communities such as the Lohars of Uttar Pradesh and the Kammari of Andhra, whose products were sought after not only all over India but also beyond her borders, are classified as Extremely Backward Classes.
There is also reason to believe the presence of phosphorus in iron was preferred because it conferred hardness. In this respect, phosphorus may prove to be slightly better than carbon, which for long has been the element of choice for alloying with iron. One hopes that in the coming years, research will unravel all the secrets of India’s corrosion-resistant iron, which - perhaps unfairly - has been eclipsed by wootz or Damascene steel that was prized in mediaeval times for making swords with exceptionally sharp cutting edges.
- 23 min read
- 1
- 0